Options
Application of in situ process monitoring to optimise laser parameters during laser powder bed fusion printing of Ti-6Al-4V parts with overhang structures
Date Issued
2023-12-15
Date Available
2024-01-15T14:24:43Z
Abstract
Enhanced levels of alloy print defects such as porosity are associated with the printing of overhang structures by laser powder bed fusion (L-PBF). This study compared the microstructure and porosity of Ti-6Al-4V overhang structures, with that observed for the bulk alloy. It was observed in the region around the overhang structure that the microstructure exhibited larger grain sizes and was less homogenous, compared to the that obtained within the bulk alloy. An increased level of porosity of up to 0.08% was also observed in the overhang print alloy, compared with the corresponding < 0.02% in the alloy bulk. It is hypothesised that these microstructural changes are associated with the excess heat generated in the overhang region, due to the decreased thermal conductivity of the powder immediately below the print layers, compared with solid alloy. During L-PBF alloy printing, in situ process monitoring of the melt pool emissions was obtained in the near-infrared range and correlated with the properties of the printed parts. This in-process data was used to assist in selecting optimal laser processing conditions, in order to help prevent melt pool overheating at the overhang. By systematically controlling the laser energy during the printing of the first fifteen layers over the overhang structure, the level of porosity was reduced, to the < 0.02% level of the bulk alloy. There was also an associated reduction in the roughness (Ra) of the overhang itself, with its Ra decreasing from 62.4 ± 7.3 to 7.5 ± 1.9 µm.
Sponsorship
Science Foundation Ireland
Other Sponsorship
SMART Eureka project APEM-AM
Type of Material
Journal Article
Publisher
Springer Science and Business Media LLC
Journal
International Journal of Advanced Manufacturing Technology
Volume
130
Issue
5-6
Start Page
2297
End Page
2311
Copyright (Published Version)
2023 the Authors
Language
English
Status of Item
Peer reviewed
ISSN
0268-3768
This item is made available under a Creative Commons License
File(s)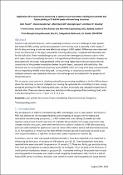
Loading...
Name
Overhang Paper - Final.pdf
Size
1.39 MB
Format
Adobe PDF
Checksum (MD5)
573fa8358b4611c362e12d184ab50475
Owning collection
Mapped collections